StarTech
Lawn Royalty
- Joined
- Feb 19, 2020
- Threads
- 113
- Messages
- 12,273
Sometimes it takes you doing follow-ups. It took me several years just to get into Gardner but with RBI it took a very short time. What is a major problem was that had a very lazy local salesman. He only lived 20 miles from me and never came out. It took firing him and hiring a new salesman before I got signed up. They are very slow to correct problems too. A couple years ago Gardner started charging 2.5% for CC use but had ACH transfers supposedly available. It took 7 months to get switch over to where I send a check after every purchase. They never setup Codis to do ACH transfers. What worst is now I have a Space Cadet for a salesperson. She calls and have no idea of what she is calling about. But RBI has Codis setup and payments get done in three days.After expressing interest in doing business with Stens early this Spring via the Internet, a representative called me. Said he would be in my area and come by my shop. No call and no show and never heard back from them. Also, they were not at the Equipment Expo this year. Business must be good for Stens…
One of the problems is turnover of sales staff. In the last ten years of being with Stens I have been thru six salespersons and only one ever visited the shop.
I only so far this year purchased about $23,000 in parts but none the vendors have over $4758 in sales. You probably not surprise how small purchases from different vendors quickly add up. Plus every year is different. So purchases from Gardner are way down but RBI is way up. Stens is down and Rotary is up.
Here is some of the top vendors here. And this don't include shipping charges.
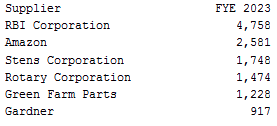