So when I went to install the flywheel, I realized I didn’t have a good way of holding it for torquing. I’d already installed the drive and clutch pulleys so I didn’t want to rely on the bolt for those. I settled on a 2.5” bolt and my 24” pipe wrench - it worked pretty well. The wrench grips the bolt and the socket I had was just a little bit smaller than the flange, so I was able to torque it without interference. Just thought that was a good tip to share.
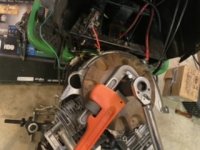
I’d been wanting to add a better drain valve for the oil, but wasn’t able to find anything I was satisfied with, so for now I settled on a 4” galvanized fitting and elbow with plug to at least keep the oil from draining/dripping onto the frame.
And finally, I started on the temp gauge install. I debated with myself for quite a while about whether or not to purchase ready made CHT kit, but it just seemed overpriced for what it was - plus I’d have to buy 2 of them because I couldn’t find anyone offering a kit with 2 probes.
I was finding thermocouples for cheap and the only visible difference between a thermocouple or a CHT thermocouple was the ring lug.
I realized the ring lug on the CHT sensor was basically just a large electrical eyelet with a thermocouple secured to it, so I took a shot at making my own. I couldn’t find any ring lugs large enough to fit around the base of the spark plugs, so I decided to try placing the probes on the bottom heat shield bolt on either head. It’s not be the most accurate place for the measurement, but again, I’m just looking for a baseline temp to use as a reference, so we’ll see how it goes.
I don’t have the gauge/reader installed yet but I readied the probes.
I’m using 2 type K thermocouples wired in parallel. I found a 5 pack on Amazon for about $15 - the plugs on them happen to be the exact same spacing as the terminals on the reader, so I’m gonna drill holes in them to accommodate the screws so I don’t have to try and secure 2 single strands of wire to them.
All I did to make the probe was insert the thermocouple into the eyelet without crimping it, then used the heat shrink to secure it. The eyelet is sandwiched between the head and heat shield with the bolt run through it
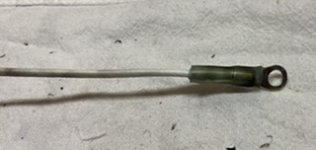
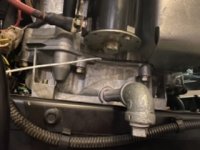