I know this is an old thread but I thought I would post an update.
Late last summer my B&S 14.5 HP engine started smoking like crazy when I mowed downhill or side hill. Checked this site and Youtube and I figure it is a blown head gasket. I limped thru the remainder of the summer with it smoking and kept a close check on the oil level. I pulled the engine out of the tractor in January thinking I would bring it home and do the head gasket repair. The mower lives at my cottage all year so removing the engine was the simplest approach to completing the repair.
I thought while I had the engine out and was tearing it apart to do the head gasket, that old pulley was going to have to come off. It is the pulley that came with the engine when I bought it used to replace the original engine that broke its connecting rod. The used engine pulley is the wrong size for the belt used on the tractor. I had kept the original pulley when I did the engine swap a few years ago. When I started this thread a few years back I was seeking advice on how to remove a frozen pulley and despite my attempts I never did get it off. I decided this time it was coming off.
So I watched a few more Youtube vids on pulley removal and tried their techniques. I drilled two holes thru the deck pulley close to the drive shaft and put my puller on it. Cranked it down as tight as I could and it was a no go. Then I turned the engine upside down so the pulley was facing up and started soaking it with Liquid Wrench for a few days. Put the puller back on and it was a no go. Then I tried to soak it in acetone and transmission fluid for a few days. Put the puller on it and it was a no go. So I decided I would make a pulley puller that could utilize my 20 ton hydraulic jack and see if that would take it off.
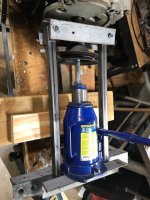
This puller pushed up on the drive shaft while pulling down on the spacer between the engine and the pulley. The pulley did not budge. The jack simply bent the 2" x 2" x 1/4" angle iron I used to make it up with. Pulley removal, still a no go!
I tried heating it with a map torch every time I put a puller on it and it had no effect at all. That was the most heat I could apply. No oxy/acetelene here for me to use.
So I finally decided I would have to grind it off. (Sorry, no pics of this process. I was afraid I would ruin the drive shaft and was concentrating on what I was doing as opposed to taking pics). I started with a thin cutting blade in my mini grinder and I cut the main portion (bell) of the deck pulley off. Then I cut the drive pulley off leaving me with just the pulley shaft that was frozen on the drive shaft. Next I cut a slot up the pulley shaft right above the key way on the drive shaft. I could hold the cutting disk above the key way and cut thru the pulley shaft without damaging the driveshaft. Then I put a small cold chisel in the slot I cut and drove it up the key way trying to open the slot wider. Nope that didn't work. I went to a point on the pulley shaft that was located 90 degrees to the key way. Using a grinding disk I started to thin the wall of the pulley shaft. I knew the inside and outside diameters of the drive shaft and the pulley shaft and kept checking the depth I was grinding into the pulley shaft with my calipers. When I was about 1/100th of an inch wider than the drive shaft I stopped grinding.
Then I went to a point on the pulley shaft directly opposite where I was grinding (i.e. 180 degrees opposite to where I first thinned the wall of the pulley shaft). I ground that spot on the pulley shaft down till I was about 1/100th of an inch wider than the drive shaft. So, at this point, I had cut a slot up the pulley shaft and weakened it in two places that were about 90 degrees each side of the key way. I put the cold chisel in the slot I cut in the pulley shaft and started driving it up the key way. The slot started to open up. Then I put a couple pry bars in the slot, pried the slot a little wider and the pulley shaft started to pop off. I kept prying and it finally let go. I hope my descriptions helps explain what I did. Without any pics it is hard to explain.
It probably took me about an hour and a half to cut the pulley completely off the drive shaft but I was going slow and careful with the mini grinder trying not to damage the drive shaft. After all that I wished I had simply cut it off to begin with and not wasted days on penetrating oil and pullers.
Oh well, the update is complete and it's time to do the head gasket. Hope this helps someone in the future.
Edit: it does not want to show the pic I have of my home made hydraulic jack puller.