Gentlemen:
I inherited a 'Garden Way' sicklebar mower made in about 1980 along with a family property. I'm sure it's been ridden hard and put away wet in it's life.
After pulling the head and re-installing, when I had to pull it again, I found that there was a surprising amount of oil on the head bolts. When I looked further I found that there was some oil pooled on the bottom of the cylinder wall (this is a horizontal shaft engine). When I wiped that oil and turned it over 4 or 5 strokes with a wrench the oil returned. Wiped it again, blocked the machine so the cylinder wall was angled up at about 10 degrees, and then turned it over 4 or 5 strokes, and there was some oil on the cylinder wall, but not enough to pool.
I've never seen this much oil come through the rings before. I've never seen enough oil get through that it seems to coat the whole of (most of) the head bolts. Am I looking at something other than a ring job? Is this somewhat normal on a 40 year old horizontal shaft? This machine would be super useful to me, but it also would only be used about 20 hours a year on personal stuff.
More background:
I inherited this acerage, and it was abandoned for a while, and when I can get this mower to run it's very useful. The thing that kicked off this investigation is that when trying to start it I get finger breaking kickbacks. On the rare occasion it starts, it runs "fine". I quoted "fine" because it's governor controlled, and even with the speed lever set to 'ludicrous' speed, where the throttle control reaches a stop preventing the throttle adjust screw from opening further, it runs at only about 3000rpm. And it also only runs for about 30 min on a full tank of gas. I'd appreciate any comments on whether those are reasonable for this engine / application.
Thank you for taking the time to look at this guys. Would love to actually fix it.
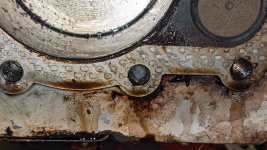
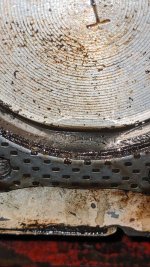
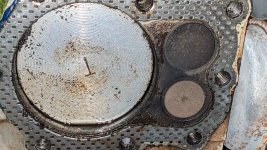
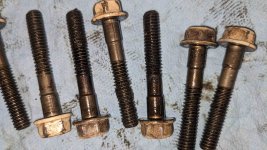