Too late.
Having a late Saturday lunch & I have already read it,,:licking:
Metallurgy 101
As a rule you do not get phase shift in aluminium - silicon casting alloys because there are no high temperature phases that can be trapped by heat treating nor triggered by overheating.
To get a phase shift, you have to cross a phase boundry line in a phase diagram like the one underneath I pinched off the web
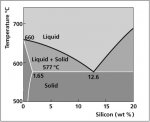
Most aluminium casting alloys used in mower heads will be in the 4% Si to 7 % Si range and if you draw a vertical line anywhere between those 2 percentages you will see these is only 1 phase, till it melts and you have 1 solid phase & 1 liquid phase.
This one phase has 2 parts, aluminium with a tiny amount of Silicon dissolved in it and Silicon.
As the temperature drops the amount of Si that can be accomodated ( dissolved ) in the aluminium drops from 1.65 to 0.5 % and this variation is what the heat treatment of Al-Si alloys utilise.
If you quench it from 577 deg then the 1.1% extra Silicon gets trapped inside the aluminium and causes it to be hard.
If you heat it up to 577 deg then hold it there for a while and allow it to cool very slowly then the extra 1.1% Si will migrate to the grain boundries and it will be full soft, which is what happens when the engine overheats.
It is also additive so consistent overheating will eventually make all the alloy fully soft.
I used the simple Al - Si example, for clarity .Cu, Be, Fe, Zn, Mn & Mg will create substantially different diagram,
In foundrys each one of those elements gets converted to a % Si called a silicon equivalent in the same manner as elements other than Zn in brasses get allocated a zinc equivalent.
Next.
Mechanical properties of metals do not have a direct & calculatable corelation to each other so a hardness of X does not mean a tensile strength of P or a creep resistance of B
However over time for a particular casting, and limited to that casting alone it will be found that if the hardness is between X & Y the creep resistace will be between A & B.
This means that on the production line you can do a hardness test on every part and provided the process is exactly the same every time be 99% sure that the creep resistance will be within spec.