I bought a 17 HP Briggs and Stratton Intek off of Craigslist to replace a 21 HP Briggs and Stratton single cylinder that blew up. When I bought it, the guy said that it had low compression and it smoked because it had so many hours on the engine. But it was in exceptionally good condition with a shiny cover and a perfectly clean block. It looked like this guy took care of his equipment. Since it was so cheap, and the cylinder bore looked flawless, I decided to take the gamble and attempt to fix it.
My initial thought was that the piston rings were probably worn out and needed to be replaced. The cylinder bore and piston is in excellent condition, with no scoring or scratches anywhere. So I took the engine apart and it is clean inside, with no significant oil sludge and no metal particles. I took out the piston and installed a brand new set of piston rings with no problems. I also went ahead and replaced the head gasket just in case that was also a problem.
I reassembled the engine and adjusted the valves to spec. However, the compression level was still almost nonexistent, measuring only 15 psi. I then thought that the valves may not be seating correctly so I proceeded to take apart the cylinder head. After I lapped the valves and cleaned it all up, I reassembled it and put it back on the engine.
This time however, there was way too much compression. The starter motor just could not move past the compression stroke. It was also exceptionally difficult to turn over by hand when it came to the compression stroke. Other than that, the engine rotates freely as it normally should. Just in case the starter motor was bad, I swapped it with another one that I knew worked fine but it did the same thing. It just barely gets passed the compression stroke.
So I kept on messing around with adjusting the valves, fiddling around with the camshaft, and even going as far as swapping the entire cylinder head with the one from the blown engine. But there was no change. Interestingly, when I hook it up my compression tester, it only measured 65 psi, which is still way too low. But it doesn't make any sense why it would have that much compression and only come up with 65 psi on the gauge. When I do turn it over, the needle on the compression tester gauge jumps up a lot every time it passes the compression stroke, which usually indicates a healthy engine. But it just stops at 65 psi and will not go any further. Just to make sure that my compression tester wasn't giving me a false reading, I tried it on another engine and it works just fine.
One thing I did notice while I was assembling the engine was that the camshaft is a bit strange. The timing mark on the camshaft gear is supposed to be in between one of the teeth. Instead, the timing mark located on one of the teeth. This was bizarre and didn't make any sense because the crankshaft gear normally has the dot on one of the teeth, so they never match up. I am not sure if this is an error from the factory or what. Another thing I noticed is a small wear mark on the very edge of one of the cam lobes. I have no idea what could have caused that to happen. The tappits look fine and don't any wear marks on them so I don't know what is going on with that. Again, I suspect it might have been a casting mistake from the factory but I honestly don't know. I will show pictures of the camshaft showing this.
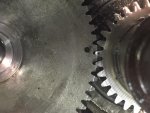
I don't think the strange wear marks on the camshaft contribute to this problem.
I am stumped as to why it is doing this. I am no stranger to building these motors, but I have never encountered this problem before. If anyone has any ideas on how to fix this, please let me know! Also if you need any more pictures of any part of the engine, let me know.